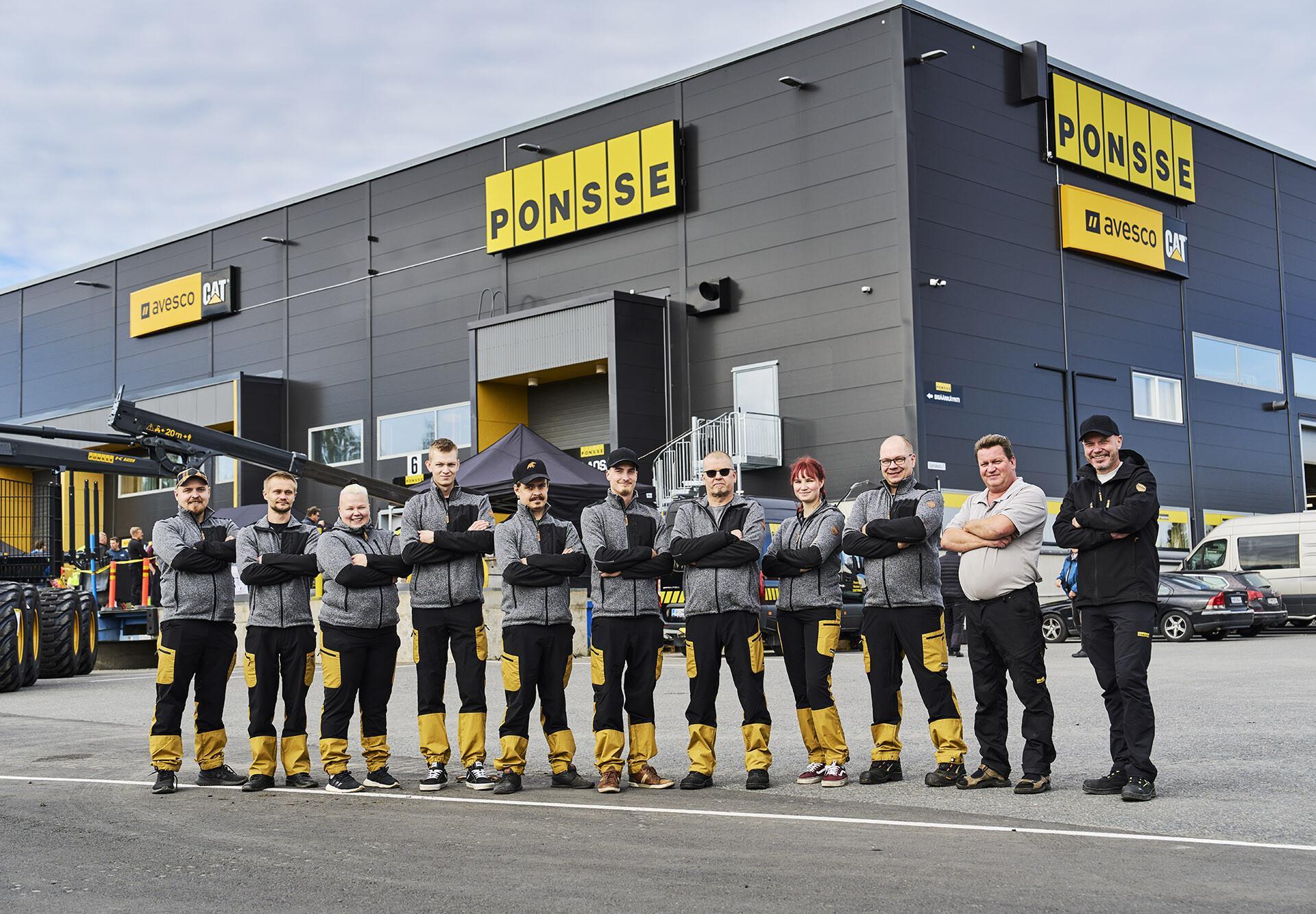
ESW guidelines improve the quality and safety of maintenance services
An effective and safe service centre provides the best possible maintenance services for customers. ESW helps identify any areas that require development and enables the continuous improvement of maintenance services. More than 600 conducted ESW audits mark an example of Ponsse’s commitment to high quality and customer satisfaction.
FULL FIVE STAR SKILLS
The audit was performed at the Kuopio service center in March 2022. It was found that the development of the service center meets the five-star criteria. Full service service center operates in Kuopio with a force of ten people.
”We moved to new premises on Sahakatu at the beginning of 2020. The premises were built according to the requirements of the modern forest machines.
“I am pleased that we have developed our service center to this point and have earned five star”, says the service supervisor of the Kuopio service center Marko Luodes.
There are 14 Ponsse’s own service centers in Finland, 11 of them have passed ESW auditing. Six audited service centers has earned five stars and five service centers four stars.
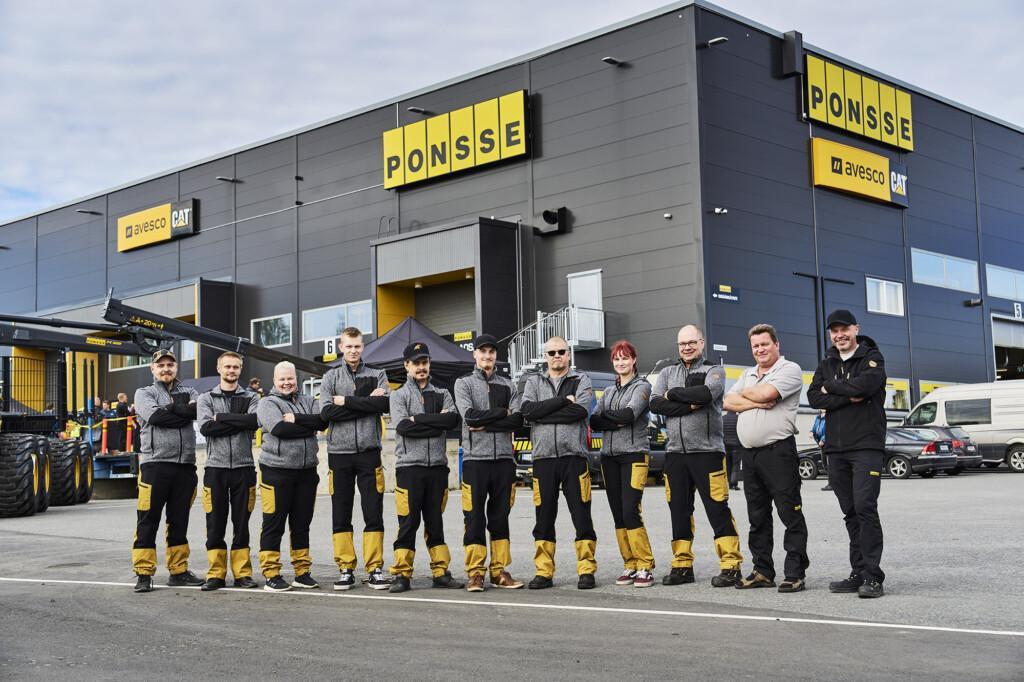
An effective and safe service centre provides customers with the best possible after-sales service.
ESW is short for Effective and Safe Workshop. It is a comprehensive set of guidelines for Ponsse’s authorised maintenance organisations, covering the activities and services of service centres.
The ESW guidelines help provide customers with services of as high and even quality as possible, regardless of where they operate and whether they acquire services from Ponsse’s service centre, retailer or contractual service partner.
“ESW is also a continuous improvement tool to develop the maintenance network globally and improve maintenance services locally,” says Harri Perätalo who is responsible for the development of Ponsse’s field maintenance and service centre operations.
What started as auditing has been developed into guidelines. The guidelines make information better available, responding to changing needs. Currently, auditing is part of a larger set of guidelines.
A small development team conducted the first three audits at Ponsse in 2011. Strengthening Ponsse’s quality image in the maintenance network was one of the starting points.
“We also needed to add visibility to local operations and regular two-way communication to our global network.”
Guidelines for various service center operations
ESW covers 28 different areas, ranging from the arrangement of the customer space and branding to the effectiveness and expertise of maintenance and spare parts processes. Key metrics include occupational safety, the environment and training.
“When it comes to ESW, we seek to identify how service centres and field maintenance operations have prepared for various factors, many of which are related to sustainability. Training is also part of sustainability and safety.”
Currently, Ponsse has 11 factory auditors, mainly maintenance professionals with various specialisations. In addition, local auditors are used in North America, Uruguay, Brazil and Sweden – in markets distant from the factory or with a large contractual service partner network.
The audit process is cooperation in which auditors and service centres work together to identify any areas for improvement.
“It is important that auditing is regarded specifically as a development tool. We want to support our service centres, not rank them. By identifying and making improvements, we can increase the quality of our services which produces the most benefits for our customers and local maintenance services,” Harri says.
Improvements after measurements
According to Harri Perätalo, the leading idea behind the ESW tool is that what can be measured can be improved. If it were not for measurements, it would be difficult to know exactly what should be developed. Once a score has been given for each area, a star rating is determined based on the results.
“For example, the lower limit for three stars is 49% of the maximum score, whereas the limit for five stars, the highest score, is 89%. A once-earned high score does not automatically stay the same forever. Continuous development is required, and the criteria may also change according to needs.”
The rating also creates motivation and positive competition. Maintenance professionals want to show what they can do.

Having worked years across the world for Ponsse, Harri has seen that customers appreciate it when a local authorised Ponsse service partner develops and improves its operations and invests in them in the long term.
“This also gives customers courage to make investments and buy machines. They can rely on Ponsse doing its best and keeping machines up and running.”
BULGARIAN MARKET LEADER SEEKING FIVE STARS
Established in 2014, Progress Technik Ltd. provides services
for its wood and forest industry customers. Its partnership with Ponsse started in 2018.
“In less than six years, we have become the market leader
and are already providing services for roughly a hundred PONSSE machines on the Bulgarian market,” says commercial director Ivan Laskov.
“It is safe to say that our success comes from our close relationship with Ponsse’s sales and marketing, as well as maintenance and spare parts services,” he says.
Progress Technik has used the ESW manual and aimed to follow it as precisely as possible. Intended for Ponsse’s authorised service centres, the ESW manual is a summary of best practices and the result of Ponsse’s long-term experience in forest machine maintenance and customer service.
“To provide the best possible service for our customers, we need to be as prepared as we can, and the ESW guidelines offer the best tool for this purpose. ESW also helps us prepare for situations we have never experienced before,” Laskov says.
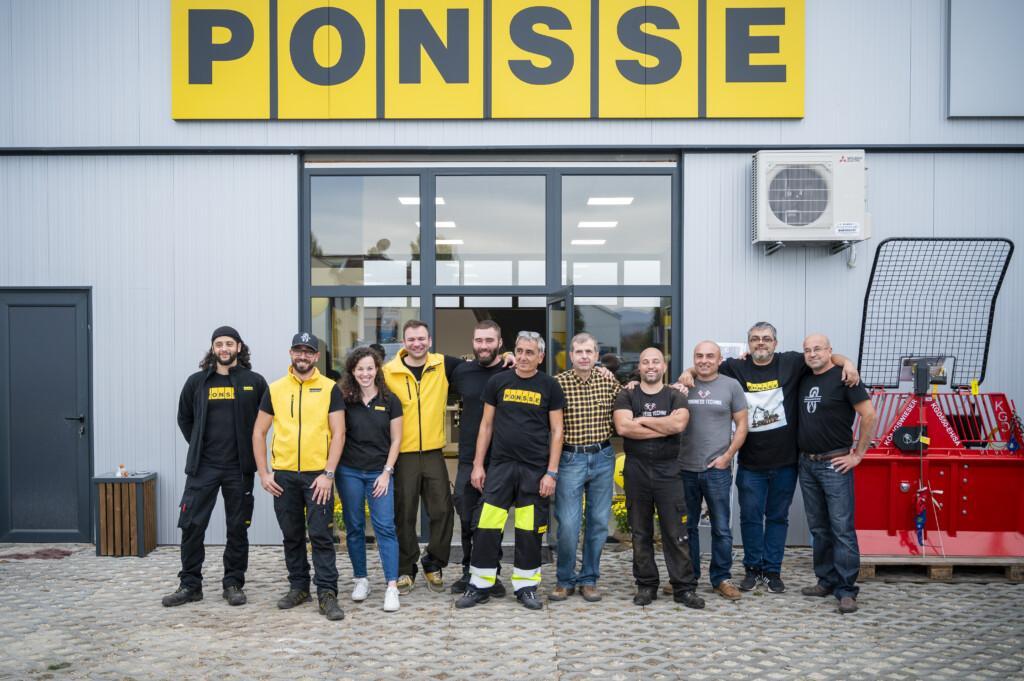
According to Ivan, the deployment of the ESW guidelines was a long and demanding process which brought along many useful experiences. The process also brought the team members closer together and motivated them, as they all sought to make it a success.
“Our service centre was given four stars. Our goal is to combine our efforts during the next three years to become a five-star Ponsse partner. We will follow the ESW guidelines as closely as possible,” Ivan Laskov says.
TEAM IN MIKKELI ACHIEVED EXCELLENT RESULTS BY WORKING TOGETHER
Ponsse’s service centre team in Mikkeli has developed its activities with great leaps forward in accordance with improvements and instructions created based on ESW audit reports. While the first ESW audit conducted eight years ago produced the result of 76% of the maximum score, the team’s performance in 2023 was excellent at 96%.
“We started from easy and affordable improvements and decided to put them into practice. Each year after that, we have also sought to complete a few more demanding projects,” says Regional Service Manager Marko Iivanainen.
During the first ESW audit, the Mikkeli service centre was still based in its former and smaller facilities.
“Even though the repair shop was cramped, we reorganised it together to make working smoother. We learned valuable lessons trying to find the right place for everything. Despite the limited space, we were able to make our operations more effective,” Marko says.
In 2019, a new building was completed for the service centre, with the repair shop being based on the ESW guidelines. The experiences gained from the previous facilities helped organise the new repair shop like no other before work was started. Working in the modern facilities is effective and safe which is also reflected in high customer satisfaction.
“When customers step in the repair shop, they can see that the space is tidy and everything has been carefully considered. The first impression is systematic, and I believe that customers can see that we have everything under control.”
Ponsse’s maintenance services are customer-driven, with customers given priority in all operations. Marko Iivanainen knows that this is why the development of operations can sometimes be forgotten in all the rush and customer activities.
“The correct moment may never come – we simply have to make time and decide to make everything right. Every hour spent will eventually repay itself through improved efficiency and smoother processes.”